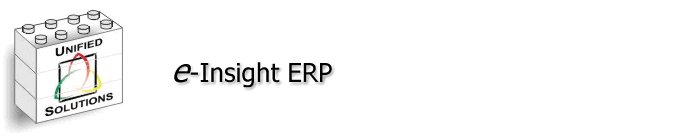
System Features
System Features Overview:
The e-Insight ERP application uses a very flexible database environment. It supports operation on Windows Servers, Novell Netware and Linux servers. The system is very scaleable and stable. The core data engine has been around for 20 plus years. It is a MultiValue environment – it allows multiple items per field, where defined, allows for variable length data fields expanding and contracting automatically and follows the real world – you have more than one address line and your buy more than one item.
The product is the OpenInsight Development environment from Revelation Software, Westwood, NJ. It allows us to build full-featured products, with less code than most other products. It also allows us to quickly build new features and functions when our customers request.
Sales Orders:
System Generated Unique Key – no duplicate numbers
Sales Order Date defaults to current day
Search Sales Orders to locate old Orders via Options Button
Start Date/Cancel Date option for Processing Orders to Retailers
User Defined Ship via Field
Choose which Warehouse to ship from
Choose from 4 defined Freight Codes
Credit Checking with auto-hold if exceed credit limit
Order Status – New/Backorder/Closed/Cancelled
Terms override on Sales Order basis – defaults to Customer assigned terms
Notes available at Sales Order and per Line basis
Terms Default from Customer Record
Sales Lines display customer part number if defined
Unit of Measure defaults from Part Master
Price defaults to Part Master List Price, will update to quantity break if there is a Customer Part Price list
Delivery and Scheduled dates allow for multiple lines
Shows Receipt and Shipment info for easy lookup for Customer Service
View Inventory, Parts Master, Customer Pricing, Part Drawing and MRP with simple button clicks in Lines
View Customer and Contact history from Sales header
View Customer Pricing
Lookup Options on fields linking to Customer controlled support tables – button or F12 key for quick access
Daily Results Snapshot – a form to display new SO for a day, AR, Receipts, PO’s, breakdown by customer, by product, and by product class, total orders, dollar value and estimated margins
Gross Profit Summaries – by customer, by product and by sales person based on sales orders and invoices and costs based on BoM standards.
Reports – there are many standard reports that can also be modified and adjusted for each organization.
There are also reports specific to historical information.
Setup – simple forms to enter data for supporting tables
Sales Person – in-house or reps, setup commission rates
Customer Pricing – set up pricing schedules for each customer by quantity breaks
Purchase Orders:
PO Number automatically assigned and is a unique number
PO Date defaults to current day
Log Buyer and/or Requisitioner Names
Start Date/Cancel Date Fields for Shipping from Vendor
Ship Via based on expandable table
Tax Rate defaults from Company Data
Vendor Order Address and Payment Address can be different
Ship to address defaults to Company Ship Address, can be overwritten
Terms Default to Vendor File
PO Type can be Standard Vendor, Outside Processing or Other
Define Scheduled Receipt Dates and Quantities for Multiple Shipments
See Receipt Information on same form for easy review
Notes can be at the header and/or line level
See Part Master, MRP Info, Account and Drawings from button clicks
See Work Orders assigned to line item
View Vendor Record and Contact information from Header Form
One form for regular PO or Outside Processing PO based on Status
Print individual or batch PO’s
Many predefined reports – all may be modified or new reports added easily
Inventory/Parts:
Every Part assigned to a Class or Group for easy reference
Every Part assigned to a Cost Class for Costing updates
Support for UPC numbers, customer part numbers, and company defined GTIN-14
Multiple Warehouses supported
Locations company-defined and assigned to a warehouse
Units of Measure very flexible – each/piece to thousands, cartons, pounds, kilograms – company can define and link together
Company-defined Inventory Transaction Reasons to standardize and group for reporting purposes
Part Type defined as Raw/Finished/Other to speed part lookups
Part has a default Unit of Measure and also allows for Alternate Unit of Measures
Flag Part as Purchased/Manufactured/Other
Track Revision Letters and Dates
Track ECO Letters and Dates
Track Stock information – Order Quantity, Lead Times, Safety Stock, Maximum Order Quantity
Enter Conversion Options – Pieces per Carton, Pounds per UoM, Counts per Pound, and Cube
Enter carton dimensions for packing and EDI requirements
Enter Preferred Vendors in Order
Enter Standard or Outside Processing Descriptions
Easily view Bill of Material, Routers, Units of Measure, MRP, Pricing and Drawings with simple mouse clicks
Parts also provide default GL Account assignments – Sales, Receiving, COGS, Inventory accounts and more
Enter Customers purchasing part and reference their part numbers
View Transactions for part and history easily – warehouse, location, quantities in and out
Receiving:
Straightforward receipts entry – system defaults receipt number and date
PO Lookup via popup list
Enter Receiving Lot numbers in this form
Enter receipt quantity – system compares to PO quantity for item
View PO with mouse click
Print Receipt list quickly
View On-Time Receipts compared to scheduled dates
Container Tracking – for receiving ocean-going/multi modal shipping containers, including shippers container number, PO’s associated, specific products, estimated and actual delivery dates.
Assign Carton Id's on receipt or create at shipment time
Shipping:
System assigns Shipment number and ship date
Easy entry of Freight Costs
Ship Via based on company defaults
Track number of cartons and weight
Ship Address defaults to Sales Order but can be overwritten on request
Quick entry of quantities from locations
Option to Invoice Shipment directly
View Sales Order Ship Schedule from Shipper
View On-Time Shipments compared to Scheduled Dates
Print Shipments quickly – individual or batch process
Consolidated Distribution Center – aggregate SO’s based on customer distribution center, start date, due dates, sorted by sales orders, ship to location of Bill To, Distribution Center or Ship To Location.
Create Shipment Records automatically from finalized Consolidation Entry
Bill of Lading – data fed from consolidation records, totals by product, by NMFC code and by customer PO, total weight, number of cartons and cube. Print consolidated Manifests
Direct Shipment details - vessel name, id, port of entry, type
Print UCC-128/GTIN labels with proper routing
Track Carton Level details of sales orders assigned, shipping Id, BoL ID, Consolidation ID, location movement, etc.
Submit EDI 753 Routing Requests and Receive EDI 754 Routing
Period Inventory
Setup Cycle counting easily
Year End Inventory Processing, including tags, reports, and such.
RMA’s:
The system has the ability to issue RMA’s with a system-generated id.
Track Customer Order Number, Invoice Number
Company Part number and Customer Part number tracking
Notes field expandable for complete causes
Track review by Quality Department, Reasons, Who Assigned to task and date
Enter detail description of review
Expandable fields for Discussion of Root Causes, Recommended Actions, Corrective Action Taken and Repair information.
Production/Manufacturing Tracking:
A strength of the system is the ability to track the manufacture of the products, including multiple machines and outside processing.
Bill of Materials
Enter Part Number then start adding components for the product
Multi-level possible
Enter Quantity required, Routing, Lead times, Alternate numbers, effective date, discontinued date, material cost
Enter Reference Notes as needed.
Generate Exploded BoM reports
Routing
Enter Route information including Production Line Number, Work Center, Operations, Labor Time, and Notes by Line. Re-sequence Lines when needed.
Work Centers
Enter Work Center name, description, total hours available, labor accounts plus rate per hour if know and needed.
Operations
Enter Operation Id, Description, time to perform the task, add the rate id for costing, type of operation.
Where Used Lookup form to see where the item is used.
Resources Entry
Use to enter other resources available to use – enter id and full description, include burden percentages and amounts
Rates Entry
Use this to assign hourly rates to equipment including any overhead percentages.
Work Orders
Use to create the Work Order for a Specified Date and quantity.
Use Multiple Notes fields to enter details for producing the product – some will print on the Work Order form, others are for internal system use.
Track Changes
Allow you to see completion information including total completed quantities
Easily see related Work In Process, Bill of Materials, Routings, Inventory, MRP and Drawings from mouse clicks on buttons.
Close Work Orders
Easily done, assigns a closing number associated with the work order number.
Displays details on Warehouse and quantities of completed products, and see raw material details.
Enter the Lot Number for the Work Order here
Report the completed quantities.
Corrective Actions Requests
Track in process status of corrective action requests (CAR’s).
Enter details on evaluation and fixes for the issue
Track who was assigned, RMA# and part information.
Set status for Open/Closed CAR
Generate reports to view details for Open/Closed/All
Customer Pricing
Use this form to enter the part number and customer plus the price for defined buckets, with override capability to defined different buckets for a particular part.
Easy look up for part and customer when handling calls or verifying current pricing for a customer.
System checks list price and customer price and will update the price for the order.
Each line has override option.
Financial System:
The product has a full-featured accounting/financial system included.
Accounts Receivable
Use the batch Invoicer process to generate invoices for all shipments for the day.
Able to override in Edit Invoice mode or to enter manual invoices
Pulls data from Sales Order
View Payment history from the AR form.
Check Credit status on entry
Aging Reports
Create EDI 810’s by Bill of Lading or all for a Date
Create EDI 810 for Factoring of Invoices
Cash Receipts
Separate module to track cash receipts and posting
Intuitive data entry – enter check number and amount, system locates outstanding AR to apply cash to.
Can apply cash multiple times to an invoice
Creates Cash Receipts journals
Individual Deposit Slips to aggregate customer receipts and/or cash
Accounts Payable
Enter Vendor Invoices via Voucher form
System calculates pay date based on invoice date and terms
Enter Vendor Invoice Number and Date
Enter PO Number or Receipt Number and system will pull in line detail
Assign Accounts on a per line basis – easy lookup via double click or F12 Option
View Past Payment on Vendor Invoice quickly
Aging Reports
Cash Disbursements
Choose bank and account to pay from – defaults to bank info from Company defaults
Easy data entry
Print Individual checks or batch mode.
Easily Reconcile disbursements
Set payable status – open/closed/hold/temporary hold/pay immediately
Checks can be top/middle/bottom and defined in company defaults
Void Open Checks
Bank Accounts
Enter Banks where accounts reside and contact information
Enter multiple Accounts per Bank
Assign default Operating Account
Tracks last check number used
Tax Authorities
Enter details for taxing authorities – state, local, school, homestead, etc.
Enter rates for taxes
Combine to get complete flexibility for tax for each state.
Terms
Pay terms easily defined and setup
Handles net days, discount days, percents
Use for Vendors and for Customer
General Ledger
Enter GL Codes easily – open format to allow sub accounts and multiple segments
Length of Code can be over 30 if needed
View GL Detail easily
Enter GL Journal quickly
Recurring Journal Entries easy to setup and reverse
Multiple Period Processing
Multi-Company setup
Print Trial Balance
Financial Statement flexibility – print or export to Excel or similar spreadsheet
Define Sum Accounts
Budgeting
Enter budget amounts by GL code for fiscal periods
Flexible viewing
Year End Processing
Follow a simple end of year step-by-step process to close the year
Keeps transactions for years
Allows for easily re-generation of prior period details and reports
Reporting:
There are over 150 standard reports in the system
More are added regularly.
Reports initially go to screen for viewing prior to sending to printer
Can be defaulted to print directly to system default printer
Reports can be Archived, create PDF’s, create HTML, export to Spreadsheet
A Development copy of the Reporting tool can be added as an extra cost option.
Administration:
Enter Users, Security and Menus from easy to use forms.
Passwords and access defined in these forms
New Menus can be easily developed for departments and specific individuals.
Updates and Changes to the system are easily applied via our Update Utility form.
Users may not have to exit the system totally when this is run, depending on type of update.
Setup:
Easily setup the system via the INIT menu – has all the forms required in order to enter the base data to start using.
Company defaults, bank accounts, GL accounts, warehouse(s), units of measure, tax information, pay terms, salespeople, customer and vendor information, part classes, cost classes, start entering part via the part master, ship via types and receipt status codes.
All the forms exist on the normal processing menus; this INIT menu just places these in one place in the correct order to configure the system quickly to be up and running.
Other System Info:
Source Code Included – you will have a complete copy of the source code of the product on a pc in your office upon implementation of e-Insight ERP. A development copy of OpenInsight required to access this information
Multi-User capable
Windows 2003/2008 Server/Windows XP Server environments supported currently, via TCP/IP protocol. Linux option available
Works with Terminal Services or Citrix configuration for multiple sites or traveling users
Scale up using IBM’s Universe for larger, multi-site installations
e-Commerce ready:
Customer/Vendor lookups
HTML, SHTML or Java Options
Requires a web server on site and running OpenInsight as well.
You tell us what you want it to look like and we will make it happen.
Spawn multiple engines to handle large requests.
XML:
Our product does XML.
XML and MultiValue are made for each other. XML is string manipulation. MultiValue is string manipulation. Hierarchical data in XML is our MultiValue strength.
XML Import/Export Utility – creates schemas and used to define new imports
Bring the data in as a string or parse into fields in the database.
Integrated with:
Loftware Print Server – print bar code labels, receipt or UCC-128 compliant, RFID-Ready when you need to meet customer demands. Easily print 1,000’s of labels per day (depends on number and speed of printers), route to local or internet attached bar code label printers from most printer manufacturers.
All bar code printing sent to Print Server for processing
Scales up for high volume, multiple printers and multiple locations
Choose which printer at time of label generation
Print over TCP/IP and Internet for offsite locations
Label formats are designed and stored in Loftware
See www.loftware.com for details.
SmartBoL from ADi Data International – print Standard VICS Bill of Lading, handles Master BoL’s and sub-BoL’s
SmartBoL maintains VICS compliant formats, custom formats
Export data to SmartBoL server to print on plain paper
Supports bar code on BoL
Wireless Scanners –
Support almost any Windows CE based scanner
Custom Menu structure for your requirements
Utilizes Internet and Web Server to interface to data
Dependant on antenna coverage in your warehouse
Option to store data to internal SD Cards if available
Use Scanner to move product to new locations
Use Scanner to assign product to Consolidation Records and BoL’s
EDI:
EDI integrated using FrEDI from User Friendly Systems
Process Daily EDI 850 Sales Orders into SO table, includes various pre-import reports
Export EDI 856 ASN’s for BoL, EDI 810 Invoices Daily
EDI format forms to allow processing by Customer
Other EDI Documents Supported includes 812, 816, 820, 824, 830, 852, 860, 864, 869, 870 and 997
Import for reporting and printing of results
Supports 4010 and 4030 standards, plus dial-up access, ftp support, vpn support and ANSI X12, AS2 and EDIFACT
Will Integrate with:
- Microsoft Office compatible for sharing data
- Reporting can be enhanced via Crystal Reports and the ODBC driver
- PDA’s such as Palm units can be used via customization process
- Supply Chain integration – let us know what your vendors require, and we can make it happen quickly. All systems are different and you cannot ‘preprogram’ the solution for every company.
- Payroll – We can integrate with various payroll applications on the market, or work with you on developing the steps to enter your payroll from third party vendors such as ADP, Paychex, Optimum Solutions etc.
Volume Estimates:
Easily handle 5,000 EDI 850 Orders per day
20-40 outbound trailers with BoL’s daily
Shipment of additional 20 trailers per day from remote warehouses
Receive 10 or more inbound shipping containers per day
Process 1,000’s of EDI 856 ASN’s and 810 Invoices per day
Largest install has approximately 25,000 skus
Tracks 390,000 unique cartons in multiple warehouses/locations, plus history on 1,000,000+
Supports multiple shipping locations for customers – approximately 9,000 ship to locations
Please contact us for further information or a demo. |